5 Types of Portable Appliance Testing Methods: Which One is Best for Your Appliances?
Testing electrical equipment is a MUST when it comes to electrical safety. Inspection and testing of equipment should be routine, especially for businesses that use their appliances daily.
When it comes to Portable Appliance Testing, PAT tests are the most common way to ensure that your electrical installations are safe for use.
However, Portable Appliance Testing has many variations. You may also need specific PAT testing equipment to do the job.
Here’s how you can differentiate each type of PAT testing and how to choose the appropriate one depending on your needs.
5 Types of PAT Testing: Uses, Equipment, Benefits
PAT testing isn’t limited to one method. There are different ways to do it, depending on the appliance you’re working with. It requires technical knowledge to do them.
Test results are confirmed based on the IET’s Code of Practise for In-service Inspection and Testing of Electrical Equipment, which states which portable appliances are safe for use.
It can be divided into five types: formal visual inspection, continuity testing, insulation testing, earth bonding testing, and functional testing.
Testing procedures may vary depending on the appliance you’re working with. You may need a proper PAT testing certification to ensure that you follow the PAT regulations involved.
Here’s a quick guide on PAT testing, its types, uses, and the equipment involved to maximise its benefits.
Visual Inspection
A formal visual inspection requires combined inspection and testing to determine any damage or misuse of an appliance, especially for stationary appliances like washing machines and vending machines.
Formal visual inspections can quickly identify the most prominent problems in portable electrical appliances. It can even help identify those which a PAT tester can’t detect.
You would need to be a fully trained and competent person to conduct this test safely. It’s not as simple as the standard user checks, especially since it requires a more thorough assessment.
You’ll have to assess the whole portable appliance. Thoroughly check its plugs, sockets, electrical supply cable, and RCDs if applicable. These are recorded for future reference.
Check if the product is used correctly and in the appropriate environment. It can be difficult to appropriately use an appliance on a construction site when it’s meant for more low-risk environments.
You can also include a lead polarity test, which isn’t performed on the appliance itself. Instead, the lead polarity test checks if all leads are wired correctly, and your extension cables are safely installed.
Continuity Testing (Earth Continuity Test)
After a visual inspection, this is the first test you perform using portable appliance testers. These are ONLY conducted on Class I appliances and extension cables.
The primary purpose is to test the connection of the item’s earth terminal to the case. While you can do combined inspection and testing with the earth resistance test, it does have some differences.
PRO-TIP: Earth continuity is only used for appliances with metal casings. Try insulation resistance tests if your appliance’s case is made of plastic.
You’ll have to access the item’s earth terminal, which can be challenging. Sometimes, testing the earth continuity from the plug on the end of the equipment lead is acceptable.
Your PAT tester would need to make contact with exposed metal parts of the appliance to get the best reading.
The Code of Practise can inform you which readings are deemed safe enough for the electrical appliance to be used.
Insulation Testing (Insulation Resistance Test)
There are many ways to conduct insulation tests on portable electrical equipment. However, if not done correctly, it can cause irreparable damage to your appliance.
Given that these tests focus more on insulation resistance, they’re used on Class I and Class II appliances, which usually have little or basic insulation.
You would need a specific insulation resistance tester to conduct this PAT test. However, you can also use a more advanced PAT tester that can help conduct the other tests on this list.
The first method is the applied voltage method, where you expose the connecting line and neutral conductors to a test voltage of 500V DC. The electric shock should be adequately insulated by the electrical equipment to pass.
The other two methods are the earth leakage and touch current methods. These two require specific PAT testers to get the needed results.
For these PAT tests, you can look into the IET Code of Practise for the minimum acceptable values for work regulations.
Earth Bond Testing (Earth Resistance Test)
Earth bonding or resistance only focuses on the conductive properties of an earthing system.
There is a specific portable appliance tester which can accommodate this resistance test along with a continuity test, making it easier for you to do the process.
This PAT test may also require an individual tester for more accurate results. Whether they’d be willing to invest in a separate tester for this one can be a business choice.
Results from this test refer to the connection between the case of your portable electrical equipment and any metal part of the appliance.
It would need to return a satisfactory result for the appliance to be safe for usage.
Functional Testing
Functional testing is usually the last kind of PAT test conducted on electrical equipment to ensure that they’re functioning as they should.
Some PAT testers come with a load test function which helps with this objective. It can depend on the type of PAT tester you’re using.
An alternative is connecting the appliance to other electrical systems to check if it functions correctly.
If there is any other malfunction during this test, they may need additional testing or repair. Any minor changes in how the equipment functions can be a hazard in the long run.
Once your appliance passes this part of the PAT test, it should be safe for use. However, it should still be constantly monitored through user checks and the occasional visual inspection as needed.
Choosing the Right Type of PAT Test for Your Needs
PAT tests are best done for certain types of equipment. Sometimes, you would need a specific test, while others would require a full PAT test.
Knowing the proper test will help you conduct the necessary ones to follow work equipment regulations sustained by the government.
Each test requires a specific amount of competence. While you don’t need to be a professional, you can get the necessary technical knowledge for each PAT test and earn a nationally recognised qualification.
All results are recorded, usually by a duty holder, to be used in future portable appliance testing.
These are the factors to consider when choosing the best PAT test for your portable equipment.
When to Conduct a Formal Visual Inspection
Formal visual inspections are usually done to have a more detailed test than simple user checks. They can easily identify up to 90% of the possible defects before you conduct any other tests.
It’s one of the most important equipment tests, especially if the electrical appliance has been labelled damaged. These damages are usually discovered during user checks.
It’s also good to conduct a formal visual inspection if there have been any modifications or repairs on the appliance.
It’s a test that helps with risk assessment and ensures that your appliance is used in the correct environment, especially for high-risk environments.
While a formal visual inspection and testing may seem like a general user check, it’s actually more thorough, as every observation is recorded and can be used as a reference for future tests.
Visual inspections still require a level of training, unlike a user check which only requires basic knowledge of the appliance and can be done by anyone who uses it.
When to Conduct an Earth Continuity Test
This test is only used for Class I equipment, which relies on an earth connection to transport power from the socket to the appliance.
Having electrical equipment made of plastic can make it difficult to do this test as it relies on exposed metal, which is why there are times when you’d have to settle for estimations closest to the earthing system.
If a Class I appliance doesn’t pass this test, you can’t move on to the next one. Any problems with its earth connection automatically affect the insulation, giving it an automatic fail for the portable appliance test conducted.
When to Conduct an Insulation Resistance Test
An insulation resistance test is best used on equipment with a plastic case. Unlike the others, these cases can’t absorb the electric shock from an earth continuity or bond test.
These can be done during the installation of new equipment or for maintenance. Over time, insulation can wear out, especially if it’s used often or in an environment with many risks.
This test is also best recommended for Class I and Class II equipment, especially since it uses different kinds of insulation that can get worn out from constant use.
Class I equipment are high-risk appliances that work with basic insulation, making them vulnerable to damage.
Class II are double-insulated equipment that needs to function properly to prevent accidents.
While Class III isn’t as dangerous as Class I and Class II, conducting an insulation test for its other factors, like plugs and wires, can be necessary to ensure that everything is still well-insulated while used in the business.
When to Conduct an Earth Bond Test
Earth bond testings are explicitly done for the grounding of the shell of your portable electrical equipment.
It should determine whether the earth conductor is in satisfactory condition and is safe for use.
Much like the continuity test, this only applies to Class I appliances with exposed metal parts. These metal parts are where you can test the bonding of the appliance.
Since you’re working with metal parts, make sure that there’s no rust on the surface. It can change the readings and cause the meter to go up, making it seem extremely dangerous for use.
When to Conduct a Functional Test
The functional test is usually conducted as the last part. It’s important to test equipment to see if they’re functioning correctly, especially if they’ve been under repair.
A functional test doesn’t always require a specific PAT tester and can easily be done by simply connecting it to an electrical system for testing.
Whether you’re working with Class I, Class II, or Class III equipment, doing a functional test is necessary, as they should function correctly for commercial use.
It should be done before using any of your portable electrical equipment, especially since it can be challenging to have the appliance malfunction at work.
Importance of PAT Testing
Anything that involves electricity can be considered potentially dangerous equipment, especially when used on a daily basis.
PAT testing can require specific equipment to inspect an appliance thoroughly. Then, a duty holder can record all findings for future reference.
How is portable appliance testing necessary, and how do these records affect how the business runs?
When conducting a portable appliance test, consider the following factors that define its importance:
- Health and Safety: A combined inspection and testing of different appliances ensure that all appliances are safe for use, especially since all industries tend to rely on electrical equipment to get their jobs done.
- Maintenance: It’s best to know when your electrical equipment needs repair, upgrading, or replacement. A PAT test helps businesses with these decisions, especially since maintaining appliances can cost a lot, depending on their damage.
- Laws: Conducting the occasional PAT test helps appliances stay compliant with legal requirements, especially in terms of safety for employees and anyone who can be exposed to the appliance.
- Reduced Risk: Knowing the state of appliances through a PAT test can help reduce risks for malfunction, fires, electric shocks, and more. Electrical appliances are hazardous despite some of their domestic purposes, making monitoring and preventing accidents essential.
- Thorough Testing: Testing electrical equipment is more than just looking at what’s on the outside. PAT testing covers visual inspections and equipment, which can determine problems with the inner workings of an appliance for a thorough test and more accurate results.
PAT testing can also come with insurance to maximise the tests’ purpose of keeping appliances safe for use.
Benefits of PAT Testing
Manufacturers and the government have encouraged portable appliance testing to ensure that any electrical equipment in a business is properly functioning.
The HSE has suggested initial intervals for conducting these tests. However, there is no strict law that a PAT test should be required for all businesses, making it easier to forget that it’s necessary.
By being aware of its benefits, businesses can easily remember its importance and how it can help them.
Here are a few of the many benefits of PAT testing and why having the occasional PAT test is a must for any business.
Easy and Affordable Electrical Testing
Getting a certification for conducting a PAT test is more accessible nowadays, making it easier for businesses to have a trained employee do the tests for them.
PAT testing equipment is also available and easy to purchase, which can be an investment along with other appliances for a business. It’s a great addition to any other accessory a business purchases with its devices.
If a business doesn’t have an employee with the technical knowledge to perform portable appliance testing, it may need to hire an external company to do this.
In the long run, the cost of PAT tests and a portable appliance tester is a great way to save money and ensure that appliances are always in tip-top shape.
Prevention of Accidents
Conducting regular PAT tests can easily help a business determine which appliances are due for repairs and replacement.
Sometimes, conducting a user check isn’t enough to determine appliance problems, which can cause an accident.
These are easy to prevent, especially since there are ways to test equipment to know when it shouldn’t be used.
It’s cheaper to do these tests as part of a business’ routine rather than paying additional fines and bills in case of accidents.
Following a Legal Requirement
Businesses are legally responsible for keeping their employees and customers safe within the company’s premises.
Any damages from faulty equipment are under the responsibility of the business or employer, which can result in fines and additional costs which can be easily avoided.
By having a routine visual inspection and portable appliance test, they can ensure that their appliances won’t be a threat to anyone. It’s a preventive measure that holds businesses liable in case of unfortunate events.
Frequently Asked Questions (FAQs)
You may have more questions on PAT testing and its different types.
We’ve gathered the most common questions to help you further understand them.
What are the Different Classes of Electrical Equipment?
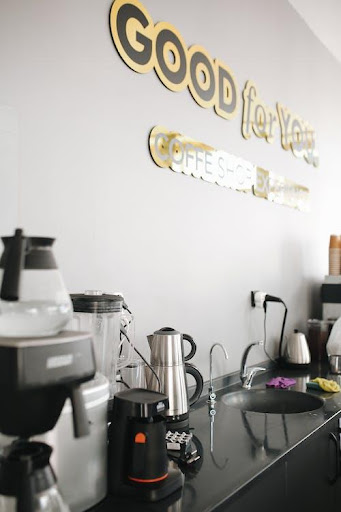
As mentioned earlier, electrical equipment has different categories that affect the tests that need to determine their safety. Class I is known to be the most high-risk, while Class III is the least.
Besides the standard user checks, which any competent worker can often do, some may require a PAT test or the use of a portable appliance tester to find any damage.
Class I equipment is any electrical equipment with an earth connection to stabilise its connection to the power source. They work with a specific power supply and fixed wiring.
Class II equipment is your double-insulated equipment. It has fewer risks than Class I, but a faulty one can still be dangerous to users.
Class III equipment usually needs the least number of PAT tests compared to the other two. They’re powered with separated extra-low voltage, which makes them much safer.
The class of your electrical equipment immediately affects the kind of electrical tests you can conduct. You’ll need further technical knowledge to understand how different they are.
Is PAT Testing a Legal Requirement?
No, conducting PAT tests isn’t a legal requirement.
However, there are different laws in place that require businesses to conduct electrical testing as necessary. It ensures that portable electrical equipment is safe for use.
PAT testers are the most accessible and affordable way to do these tests whenever necessary. They help businesses comply with their legal responsibility to their employees and customers.
Those who interact with electrical appliances on a daily basis would need the necessary training for these tests.
While any competent person can do the basic visual inspections, taking additional PAT testing courses may be necessary.
What Are PAT Testing Stickers?
After a PAT test, a duty holder records the results on whether the appliance is safe for use. They are labelled with stickers with a pass/fail system.
PAT testing stickers are used as a reference by the employees and management to know if these appliances can be used on the job.
These stickers are also not legally required, much like a PAT test. However, they’re the best way to differentiate safe appliances from dangerous ones, especially in a busy workplace.
Any appliance labelled with a fail sticker shouldn’t be used. These should be replaced or repaired as soon as possible.
If the appliance is repaired, another PAT test must be conducted to ensure the appliance will be safe for use despite the modifications.
Conclusion
A faulty appliance is a safety hazard. It can endanger the people in a business and everything you’re operating. Work regulations use PAT testing and regular inspections to avoid this.
Conducting the necessary PAT testing for portable electrical appliances ensures that your equipment is always safe.